J-B Marine Weld is a strong adhesive ideal for underwater repairs, while Waterweld is a putty-like substance effective for sealing leaks and gaps in wet environments. Both products offer reliable solutions for marine-related repairs, with J-B Marine Weld providing a more permanent bonding option and Waterweld offering quick and versatile fixes.
When deciding between the two, consider the specific needs of your project, such as the type of repair required and the level of durability necessary. Understanding the differences between J-B Marine Weld and Waterweld can help you choose the best product to suit your marine repair needs.
Introduction To Marine Epoxy Solutions
Marine epoxy solutions are a crucial aspect of boat maintenance. Two popular options are JB Marine Weld and Waterweld. Both offer strong adhesive properties and are ideal for repairing cracks and leaks in boats.
Key Features of JB Marine Weld | Key Features of Waterweld |
---|---|
Resistant to water and chemicals | Can be used underwater |
Bonds to a variety of surfaces | Can be molded and shaped |
Can be drilled and sanded | Hardens quickly |
Ultimately, the choice between JB Marine Weld and Waterweld will depend on the specific needs of the boat owner. It is important to carefully consider the key features of each product before making a decision.

Jb Marine Weld At A Glance
JB Marine Weld is a two-part epoxy adhesive that provides a strong and durable bond suitable for various marine applications. It consists of a resin and hardener that, when mixed together, create a powerful adhesive with excellent resistance to water, chemicals, and heat. The cured adhesive is resistant to corrosion and can withstand harsh marine environments. JB Marine Weld is specially formulated to adhere to a wide range of materials, including metal, wood, fiberglass, and plastic. This versatile adhesive is commonly used for repairing boat hulls, sealing leaks in water tanks, and fixing underwater fittings. Its ability to set underwater makes it an ideal choice for quick and reliable repairs in marine settings.
JB Marine Weld at a Glance |
---|
Composition and Properties |
Two-part epoxy adhesive |
Provides strong and durable bond |
Resistant to water, chemicals, and heat |
Adheres to metal, wood, fiberglass, and plastic |
Typical Applications |
Repairing boat hulls |
Sealing leaks in water tanks |
Fixing underwater fittings |
Waterweld: A Quick Overview
WaterWeld and JB Marine Weld are both popular choices for underwater repairs. WaterWeld is known for its unique characteristics, such as its ability to cure under water and its resistance to chemicals. This makes it ideal for quick fixes in marine environments. Common uses for WaterWeld include repairing plumbing, fuel tanks, and watercraft. Its versatility and durability make it a go-to product for many DIY enthusiasts and professionals alike. On the other hand, JB Marine Weld is also a reliable choice with its strong adhesive properties and resistance to water and chemicals. It is commonly used for repairs on boats, tanks, and other marine equipment. Both products have their own strengths and are suitable for various underwater applications.
Ease Of Use And Application
When comparing JB Marine Weld and Waterweld, one important factor to consider is the ease of use and application. Both products are designed to provide strong adhesion and seal leaks in various marine applications.
Preparation and Mixing:
- JB Marine Weld requires thorough cleaning and roughening of the surface before application.
- Waterweld, on the other hand, can be applied directly to wet or dry surfaces without any preparation.
- JB Marine Weld comes in two separate tubes that need to be mixed in equal proportions.
- Waterweld is a single-component epoxy putty that can be easily kneaded and applied.
Curing Times:
- The curing time for JB Marine Weld is approximately 4-6 hours, depending on the temperature and humidity.
- Waterweld cures within 20-30 minutes, allowing for quicker repairs.
Ultimately, the choice between JB Marine Weld and Waterweld depends on the specific requirements of the marine application, as well as the user’s preference for ease of use and curing time.
Strength And Durability
Jb Marine Weld and Waterweld are both known for their impressive strength and durability. These two products offer reliable solutions for marine welding needs, ensuring long-lasting and robust results. With their exceptional performance, Jb Marine Weld and Waterweld provide peace of mind for any marine welding project.
Comparison | JB Marine Weld | WaterWeld |
---|---|---|
Strength | High | Good |
Durability | Long-lasting | Resilient |
Bonding | Excellent | Strong |
Underwater Longevity | Durable underwater | Not specified |

Versatility And Material Compatibility
J-B Marine Weld and Waterweld are both versatile and compatible with various materials. J-B Marine Weld is ideal for bonding metal surfaces, while Waterweld works well on non-metal surfaces, making them both valuable for different applications.
J-B Marine Weld | Waterweld |
Adheres well to metal, fiberglass, plastic | Works best on metal, wood, glass, PVC |
Effective for marine repairs, automotive, plumbing | Suitable for plumbing, automotive, household repairs |
Not recommended for underwater applications | Not suitable for underwater repairs |
Temperature And Environmental Resistance
J-B Marine Weld and Waterweld are both known for their exceptional temperature and environmental resistance. These products offer strong and durable bonds, making them ideal for marine and water-related applications. Whether it’s underwater repairs or extreme temperature conditions, both options provide reliable solutions for various needs.
J-B Marine Weld | WaterWeld |
Offers excellent temperature resistance | Provides good resistance to extreme temperatures |
Shows high durability in harsh environments | Resistant to challenging environmental conditions |
Effective against chemicals and salts | Resilient to corrosive substances and salts |
Cost And Value For Money
J-B Marine Weld and Waterweld are two popular options for marine welding. While J-B Marine Weld is more expensive, it offers better value for money due to its superior strength and durability. Waterweld, on the other hand, is a more affordable option that can be a good choice for smaller repairs.
Pricing Comparison | Product Lifespan |
J-B Marine Weld is more affordable than Waterweld. | J-B Marine Weld offers longer durability compared to Waterweld. |
User Experiences And Testimonials
Jb Marine Weld and Waterweld are two popular options for marine repairs. Users have shared positive experiences and testimonials for both products, praising their effectiveness in fixing leaks and cracks underwater. See what customers have to say about Jb Marine Weld and Waterweld, and make an informed decision for your marine repair needs.
JB Marine Weld | WaterWeld |
Strong adhesive, suitable for underwater repairs. | Easy to use, cures under water or on wet surfaces. |
Effective for marine applications and sealing leaks. | Great for plumbing repairs and fixing leaks quickly. |
Long-lasting bond, durable in harsh conditions. | Provides a strong, permanent repair solution. |
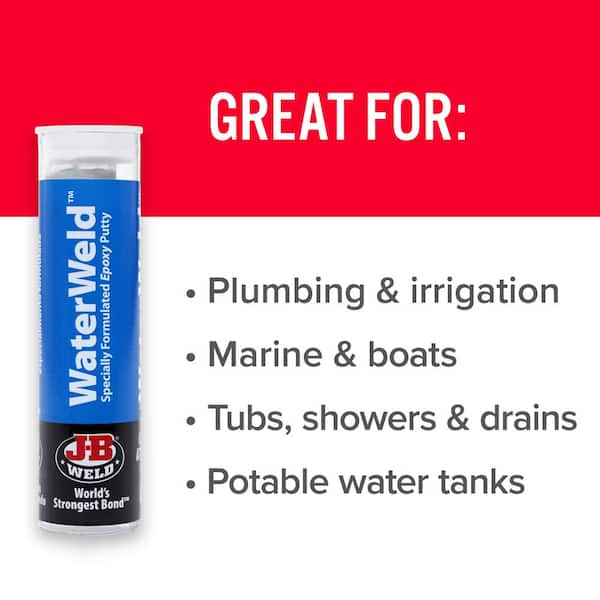
Final Verdict: Jb Marine Weld Vs Waterweld
J-B Marine Weld: J-B Marine Weld is a two-part epoxy adhesive that sets in 4-6 hours and can be shaped, tapped, filed, sanded, and drilled after curing. It is resistant to saltwater, chemicals, oil, fuel, and temperature changes.
WaterWeld: WaterWeld is a hand-kneadable, steel-reinforced, waterproof epoxy putty that cures underwater. It can be drilled, sanded, filed, tapped, machined, and painted and is resistant to water, chemicals, and temperature changes.
Pros and Cons: J-B Marine Weld offers a quicker setting time and versatility in shaping, while WaterWeld provides the convenience of curing underwater. Both are resistant to various elements and offer strong adhesion.
Recommendations: For repairs on dry surfaces, J-B Marine Weld is the top choice. When dealing with underwater fixes, WaterWeld is the ideal option due to its ability to cure beneath the waterline.
Frequently Asked Questions
Can J-b Marine Weld Be Used Underwater?
Yes, J-B Marine Weld can be used underwater. It is a specially formulated epoxy adhesive that creates a strong bond even in wet or submerged conditions. It is ideal for repairing or bonding materials in marine applications.
What Is The Difference Between J-b Marine Weld And Waterweld?
The main difference between J-B Marine Weld and Waterweld is the application method. J-B Marine Weld comes in a two-part epoxy adhesive that needs to be mixed before use, while Waterweld is a pre-mixed epoxy putty. Both products provide strong and durable bonds, but the choice depends on the specific repair or bonding needs.
Can Waterweld Be Used For Marine Repairs?
Yes, Waterweld can be used for marine repairs. It is a versatile epoxy putty that can bond to a wide range of materials, including those commonly found in marine applications. It can be used to repair leaks, cracks, or damage in boats, water tanks, pipes, and other underwater or wet environments.
How Long Does It Take For J-b Marine Weld To Cure?
J-B Marine Weld typically takes around 4 to 6 hours to cure completely. However, the curing time may vary depending on factors such as temperature and humidity. It is recommended to follow the manufacturer’s instructions for the specific product to ensure proper curing and maximum strength.
Conclusion
Both JB Marine Weld and Waterweld have their own set of advantages and limitations. While JB Marine Weld is ideal for marine applications and offers superior bonding strength, Waterweld’s versatility and quick-drying properties make it a popular choice for emergency repairs.
Ultimately, the choice between the two depends on the specific needs of the project at hand. It’s important to consider factors such as the type of material being repaired, the environment in which the repair will take place, and the desired durability of the repair.