J-B Weld offers comparable strength to welding for bonding metal surfaces effectively. However, welding typically provides a more permanent and structurally sound connection.
The strength of J-B Weld lies in its versatility and ease of use for various materials and applications, offering a convenient alternative to welding for certain projects. Welding, on the other hand, requires specialized equipment and expertise but results in a stronger and more durable bond for heavy-duty applications.
Both methods have their advantages and are chosen based on the specific requirements and constraints of the project at hand.
Introduction To Jb Weld And Traditional Welding
JB Weld is a popular brand of epoxy adhesive that is commonly used for various bonding applications. Unlike traditional welding, which involves melting metals together, JB Weld creates a strong bond by hardening and adhering to the surfaces it is applied to. It is a versatile solution that can be used for a wide range of materials, including metal, plastic, wood, and more.
JB Weld consists of two components – a resin and a hardener. When these two components are mixed together, a chemical reaction occurs, resulting in a strong and durable bond. The curing time can vary depending on the specific product, but once fully cured, JB Weld offers excellent strength and resistance to heat, chemicals, and vibrations.
Traditional welding, on the other hand, involves melting metals together using high temperatures. This process requires specialized equipment and skilled welders who can manipulate the molten metal to create a strong joint. Welding is commonly used in industries such as construction, automotive, and manufacturing, where the strength and integrity of the metal joints are crucial.
In summary, JB Weld provides a convenient and effective alternative to traditional welding for various bonding needs. It offers excellent strength and durability, making it a popular choice among DIY enthusiasts and professionals alike.
Comparing Bonding Processes
When comparing bonding processes, it’s essential to consider the strengths and weaknesses of each method. J-B Weld offers a powerful alternative to traditional welding by utilizing a chemical curing process that creates a durable bond. This method eliminates the need for melting metals, making it a versatile solution for a wide range of applications. Whether you’re working with metal, wood, plastic, or other materials, J-B Weld provides a reliable and efficient bonding option. By understanding the differences between chemical curing and melting metals, you can select the most suitable application techniques for your specific project.
Material Suitability
Jb Weld Strength Vs Welding is a crucial factor in determining the material suitability for different applications. When it comes to metals and alloys, traditional welding techniques may offer higher strength, but J-B Weld provides a versatile and effective alternative for joining dissimilar metals and repairing cracks or porosities. On the other hand, for plastics and composites, J-B Weld offers distinct advantages over traditional welding methods, as it can bond different types of plastics and composites with exceptional strength and durability. The versatility and strength of J-B Weld make it an excellent choice for various material combinations and repair applications.
Strength And Durability
Jb Weld is a popular choice when it comes to bonding metals and other materials. It offers exceptional strength and durability, making it an excellent alternative to traditional welding methods. When comparing the strength of Jb Weld versus welding, two important factors to consider are tensile strength and shear strength.
Tensile strength refers to the maximum amount of tensile stress a material can withstand without breaking. Jb Weld has been tested and proven to have high tensile strength, allowing it to withstand significant force and pressure.
Shear strength, on the other hand, refers to a material’s ability to resist forces that cause it to slide or shear apart. Jb Weld also excels in this aspect, providing strong adhesion and preventing separation.
In terms of longevity under stress, Jb Weld proves to be highly reliable. It maintains its strength even under continuous stress and can withstand extreme conditions without compromising its durability.
Overall, Jb Weld offers a viable alternative to traditional welding methods, providing exceptional strength, durability, and longevity under stress.
Temperature Resistance
J-B Weld offers superior temperature resistance compared to traditional welding. The strength and durability of J-B Weld make it a reliable choice for withstanding high temperatures, outperforming traditional welding methods in many applications.
Temperature Resistance | High-Temperature Performance J-B Weld exhibits exceptional strength and resilience at high temperatures, making it suitable for various industrial and automotive applications where extreme heat is a factor. Its ability to withstand temperatures up to 600°F sets it apart from traditional adhesives and sealants. |
Low-Temperature Limitations However, it’s important to note that J-B Weld may not perform optimally in extremely low temperatures. At temperatures below 40°F, its bonding and adhesive properties may be compromised, which should be considered when selecting an adhesive for applications in cold environments. |
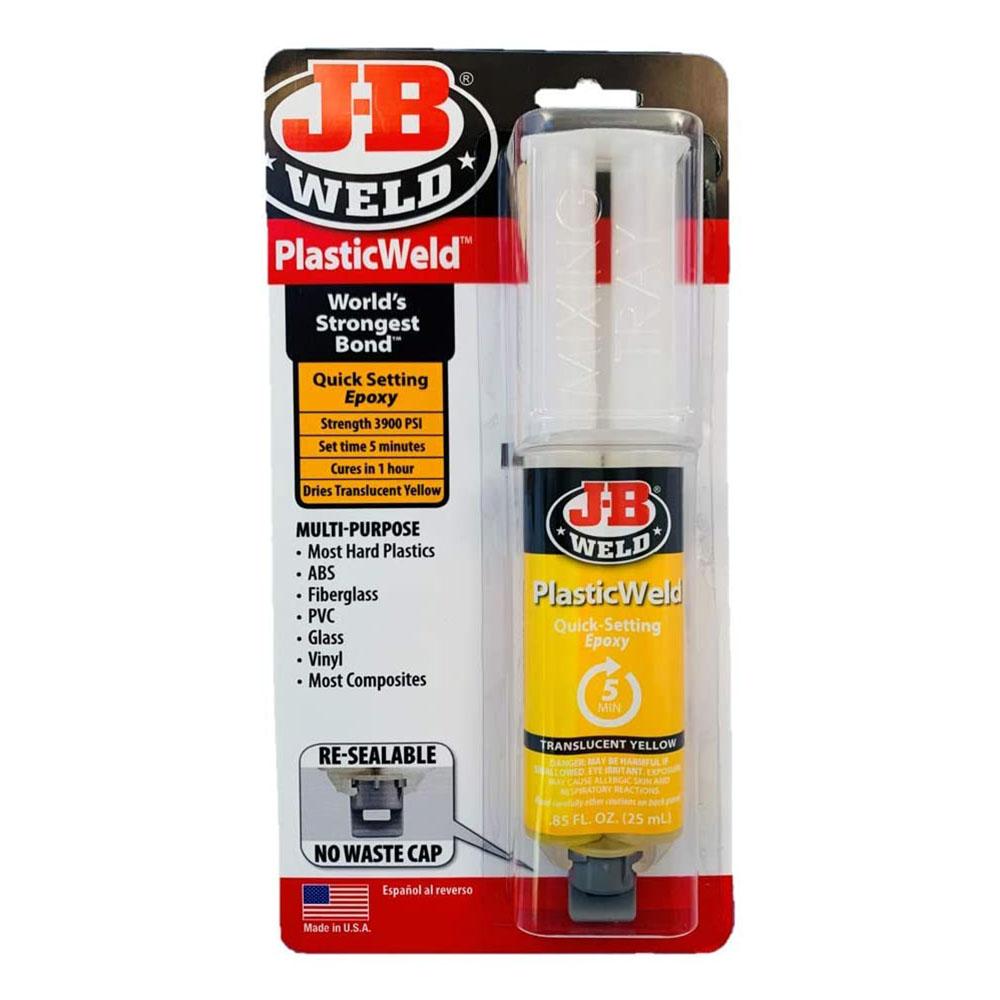
Ease Of Use And Accessibility
Jb Weld offers a superior ease of use and accessibility compared to traditional welding methods. With its simple application process and ability to bond various materials, Jb Weld provides a strong alternative for those seeking reliable strength without the complexities of welding.
Skill Level Required | Tools and Equipment Needed |
Basic skills suffice for Jb Weld; welding demands expertise. | Jb Weld: gloves, applicator, surface preparation; Welding: welding machine, protective gear. |
Cost Implications
Comparing the cost implications of Jb Weld strength vs welding is a crucial decision. While Jb Weld is cheaper and easier to handle, welding provides a stronger bond. It ultimately depends on the project’s requirements and budget.
Initial Investment | Maintenance and Repairs |
JB Weld has lower initial cost compared to welding equipment. | Maintenance for JB Weld is minimal and easy to handle. |
Welding requires significant upfront investment in machinery. | Repairs with welding may be costly and time-consuming. |
Environmental And Safety Considerations
Considering the environmental and safety implications, Jb Weld is a strong alternative to welding. With its easy application and high strength, it eliminates the need for hazardous materials and reduces the risk of injury.
Toxicity and Health Risks | Ecological Impact |
J-B Weld has minimal toxicity, posing low health risks. | Its environmental impact is generally low due to its non-toxic nature. |
Always use J-B Weld in a well-ventilated area to minimize exposure. | When disposed of properly, it has minimal impact on the ecosystem. |
Applications In Industry And Diy
J-B Weld provides exceptional strength comparable to welding, making it ideal for both industrial applications and DIY projects. Its durability and versatility make it a popular choice for various bonding needs.
Jb Weld Strength Vs Welding |
Applications in Industry and DIY |
Professional Uses |
In industries, J-B Weld is valued for its durability and reliability in high-stress applications. |
For professional welders, it serves as a quick fix for emergency repairs on metal components. |
Homeowners and DIY enthusiasts opt for J-B Weld for sealing leaks and fixing household items. |
Case Studies And Performance Comparisons
J-B Weld is a two-part epoxy adhesive that is known for its incredible strength and versatility. It has been extensively tested and compared to traditional welding methods in various real-world scenarios. Case studies have shown that J-B Weld can withstand extreme conditions and has a high tensile strength. Expert opinions and tests have consistently demonstrated its ability to provide durable and long-lasting bonds, making it a reliable alternative to welding. In performance comparisons, J-B Weld has proven to be a cost-effective solution, offering strong and resilient bonds without the need for specialized equipment. These findings highlight the remarkable performance of J-B Weld in comparison to traditional welding techniques, making it a popular choice for a wide range of applications.
Future Of Bonding: Innovations And Trends
With the rapid advancements in technology, the future of bonding solutions looks promising. Emerging technologies are revolutionizing the way we bond materials together, providing more efficient and reliable results.
One of the key trends in bonding solutions is the rise of nanotechnology. Nanoparticles are being used to enhance the strength and durability of bonds, making them resistant to various environmental factors.
Another innovation in bonding solutions is the development of smart adhesives. These adhesives have the ability to adapt and self-heal, making them ideal for applications in industries such as aerospace and automotive.
Furthermore, the use of 3D printing in bonding is gaining traction. It allows for the creation of complex structures with precise bonding points, enabling the production of lightweight and high-strength components.
As for predictions, we can expect to see advancements in bio-inspired bonding solutions, taking inspiration from nature’s own adhesion mechanisms. This could lead to the development of adhesives that are not only strong but also environmentally friendly.
In conclusion, the future of bonding solutions is bright, with emerging technologies and innovative trends shaping the way we bond materials together. These advancements will undoubtedly lead to stronger, more efficient, and sustainable bonding solutions.
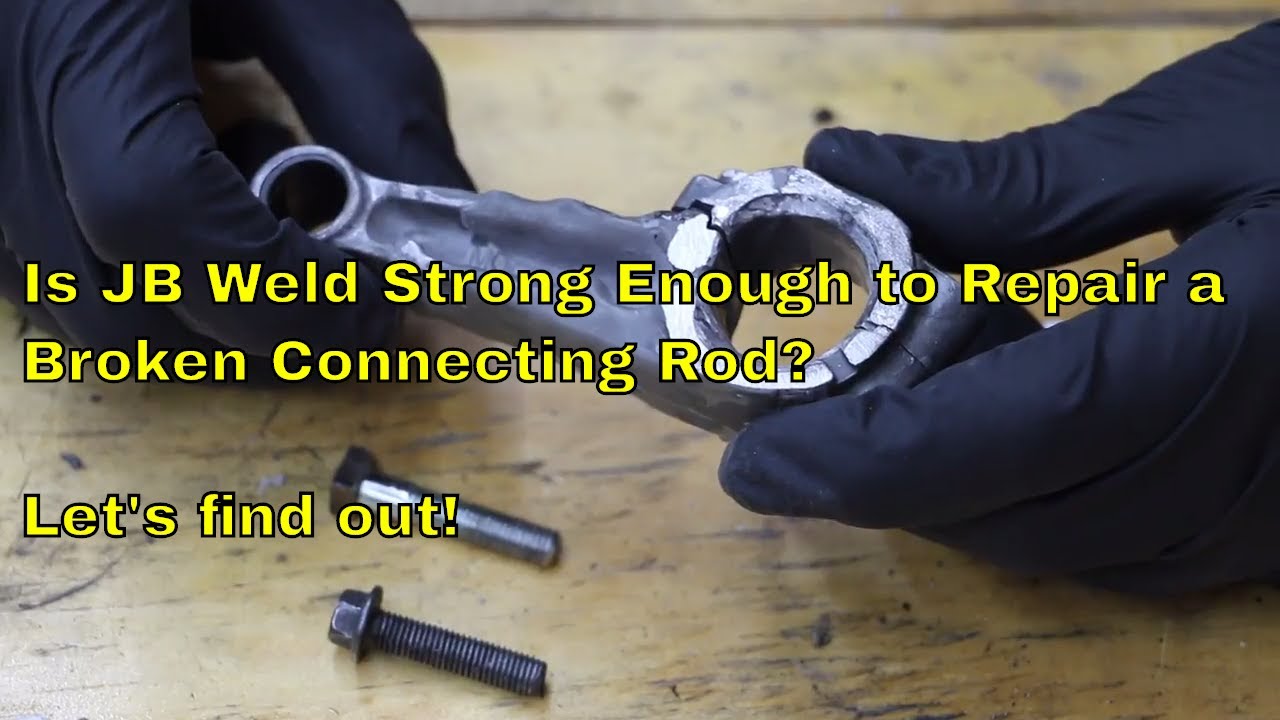
Conclusion: Choosing The Right Bonding Method
Comparing JB Weld strength to welding methods is crucial for selecting the right bonding technique. Understanding their differences helps in achieving optimal results for various projects. Consider the specifics of each method to ensure the strongest and most durable bond for your application.
J-B Weld Strength | Welding |
J-B Weld provides strong and durable bonds, suitable for a wide range of materials. | Welding is a permanent bonding method, ideal for metal fabrication and repairs. |
Adhesive vs Fusion | Strength and Flexibility |
J-B Weld offers an adhesive bond, while welding involves fusion of materials. | For strength, welding excels, but J-B Weld provides flexibility in bonding dissimilar materials. |
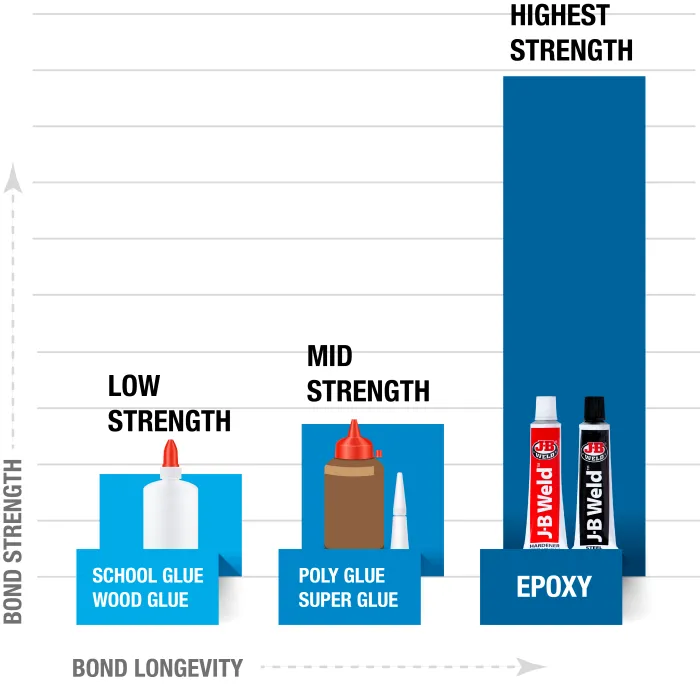
Frequently Asked Questions
Is Jb Weld Stronger Than Welding?
JB Weld is a two-part epoxy that is designed to bond and repair various materials. While it has impressive strength, it is not stronger than welding. Welding is a process that melts and joins two pieces of metal, creating a bond that is often stronger than the metal itself.
Can Jb Weld Replace Welding?
JB Weld can be used as a temporary solution for welding, but it cannot replace welding entirely. Welding creates a permanent bond between two pieces of metal, while JB Weld creates a strong adhesive bond. Welding is necessary for structural repairs, while JB Weld is best for non-structural repairs.
What Are The Advantages Of Using Jb Weld?
JB Weld is a versatile adhesive that can bond and repair a variety of materials, including metal, plastic, and wood. It is easy to use, dries quickly, and is resistant to water, chemicals, and heat. JB Weld is also affordable and can save you time and money on repairs.
When Should You Use Welding Instead Of Jb Weld?
Welding should be used for structural repairs and for joining two pieces of metal together. JB Weld should be used for non-structural repairs and for bonding materials that cannot be welded. If you need a permanent and strong bond, welding is the best option.
Conclusion
The comparison between J-B Weld and welding reveals that both methods have their strengths and weaknesses. J-B Weld offers a quick and affordable alternative to welding for small repairs, but welding is still the go-to method for larger and more complex repairs.
However, it’s important to consider the specific needs of the project before deciding which method to use. By weighing the pros and cons, you can make an informed decision and ensure a strong and long-lasting repair.